The Hirota Tsumugi Blog
- 2019.07.25
- Shina-fu Linden Fabric | Japanese Oldest Textile Tradition
Shina fu is a ancient Japanese fabric well known along with Basho-fu and Kudzu-fu, made of Shina Linden, a deciduous tree native to the north part of Japan.
It is estimated that the cloth is well-used across the Northern part of Japan from the prehistoric time as daily and work wears, or bags. It was one of the most common cloth before the spread of hemp and cotton in Japan.
Due to the spread of hemp and cotton use, Shina-fu traditions have dramatically disappeared. But even today, it’s miracle that 3 remote mountain villages on the border between Yamagata and Nigata prefecture keep the oldest Shina-fu tradition.
The villages (Yamakumada, Ikazuchi, and Sekigawa) are completely isolated, located very deep in the mountains, where takes 4~5 hours to walk from the nearest rail station. In winter time, snow reaches thickness of 3 meters.
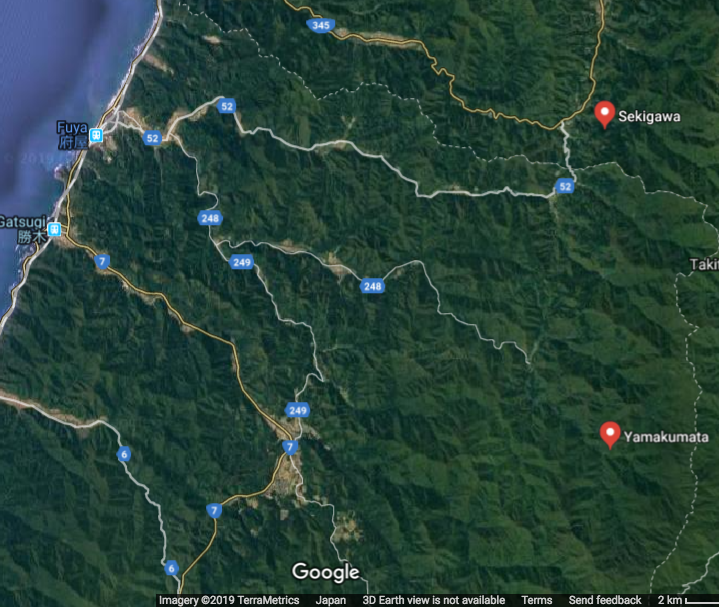
The villages (Yamakumada, Ikazuchi, Sekikawa) are about 20 km far away from the coastline town.
In the long winter of agricultural off season, their husbands go away to work at town and wives left behind were spinning yarn and weaving all day long everyday.
Today, obviously there are no successors and younger generation in the villages. Moreover, the villages are too small to about to be disappearing. The main craftspeople in the villages are mostly more than 80 years old now.
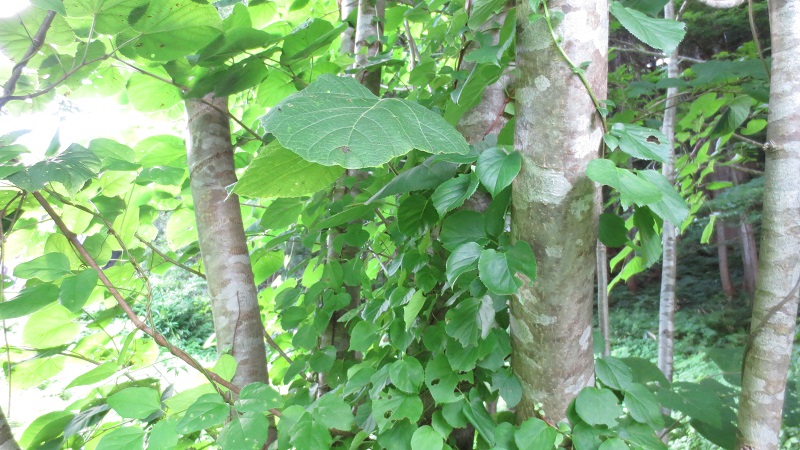
Linden trees grow naturally at valley or a slope in the mountains. The rainy season in July is suitable for pearling away the barks.
Linden trees grow on a slope near the humid riversides or valleys. During the rainy season, Linden bark is soft and relatively easy to peel away. So male villagers go into the mountain for the logging and peeling process. 8~10 years old trees are selected.
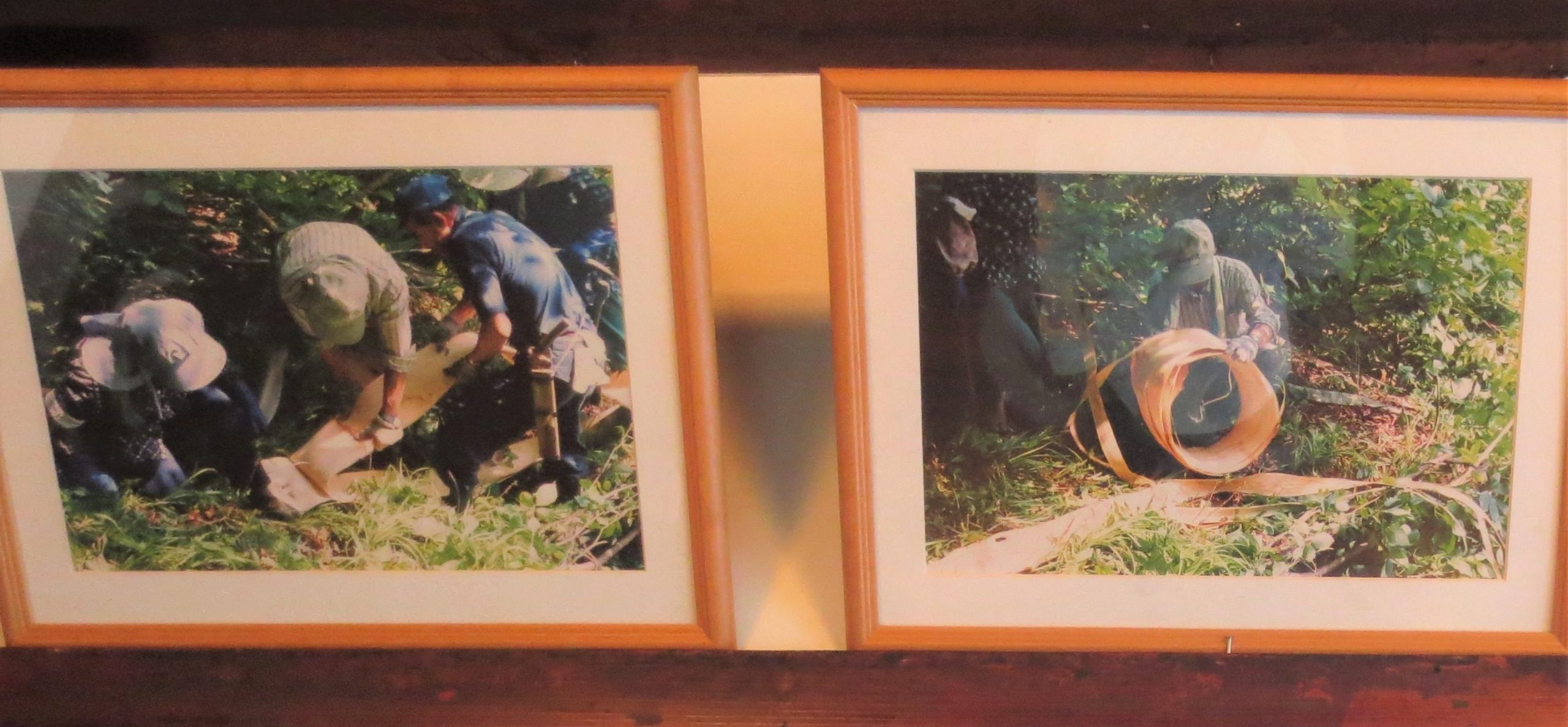
Male villagers cut down and peel away the bark on the spot, and the inner softer skin is split away from the outer hard bark.
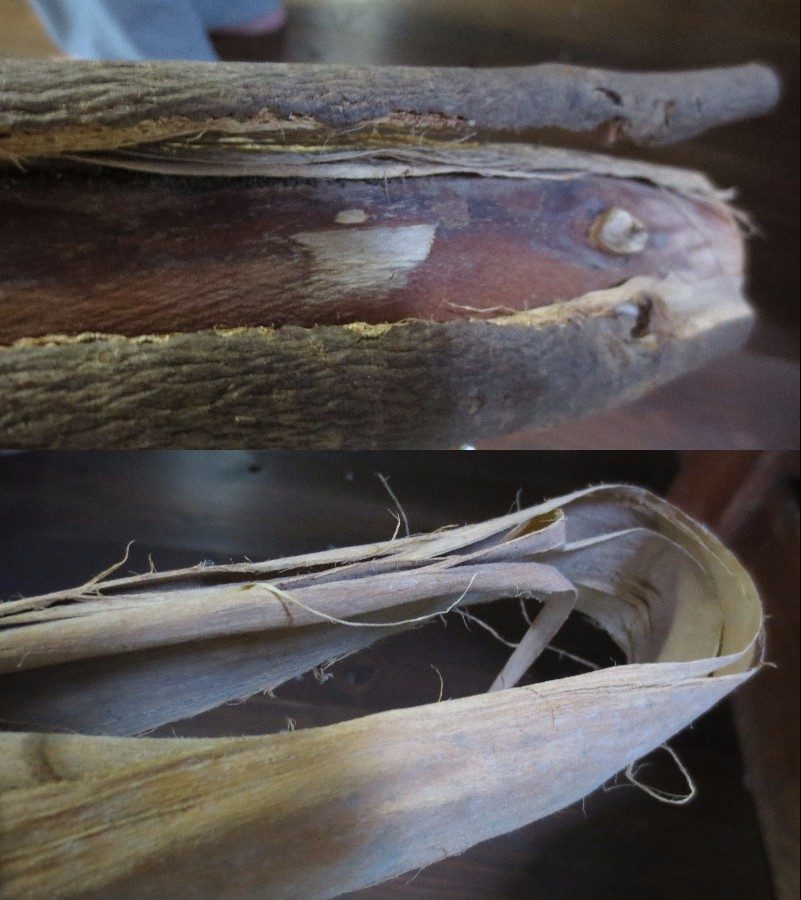
The outer bark and inner skin.
The inner skin is carried down from the mountain to the village. Then in August, the inner bark is immersed in water for 2 days and boiled in wood ash lye for 2 to 3 days.
It is then brushed up in river with stone or bamboo in order to remove impurities and extract soft, wide band-like skin.
Then, it soak in and being fermented in rice bran for 2 days, in order to soften as well as bleach the fibers. Finally, it is split up finely by fingers into 2mm wide fibers.
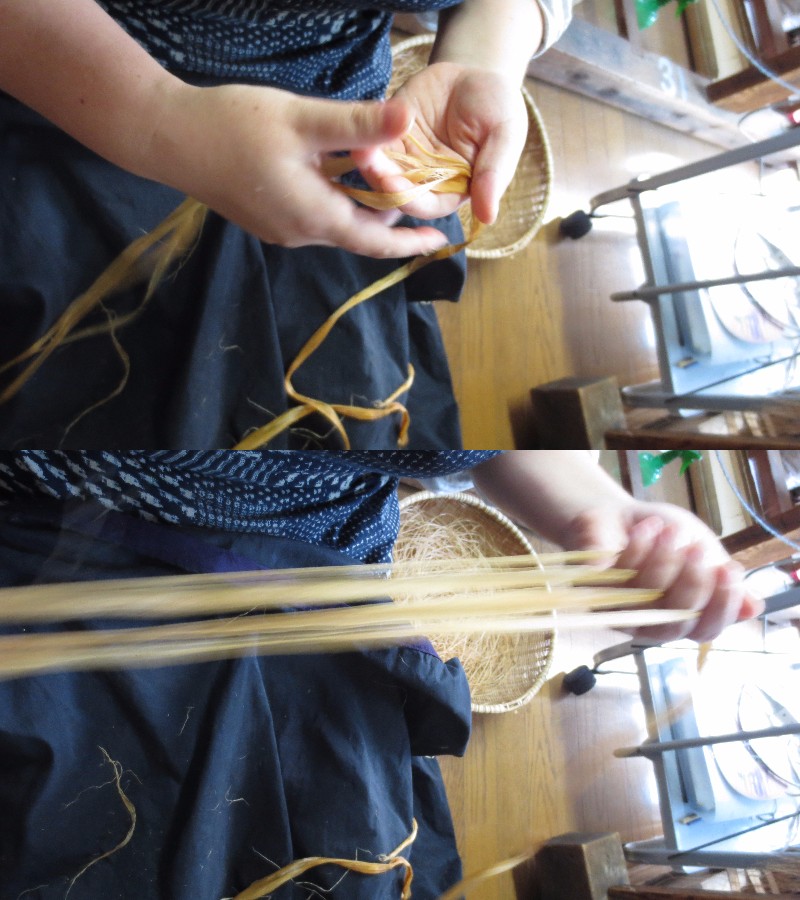
Split up fibers into 2m wide fibers by a female artisan
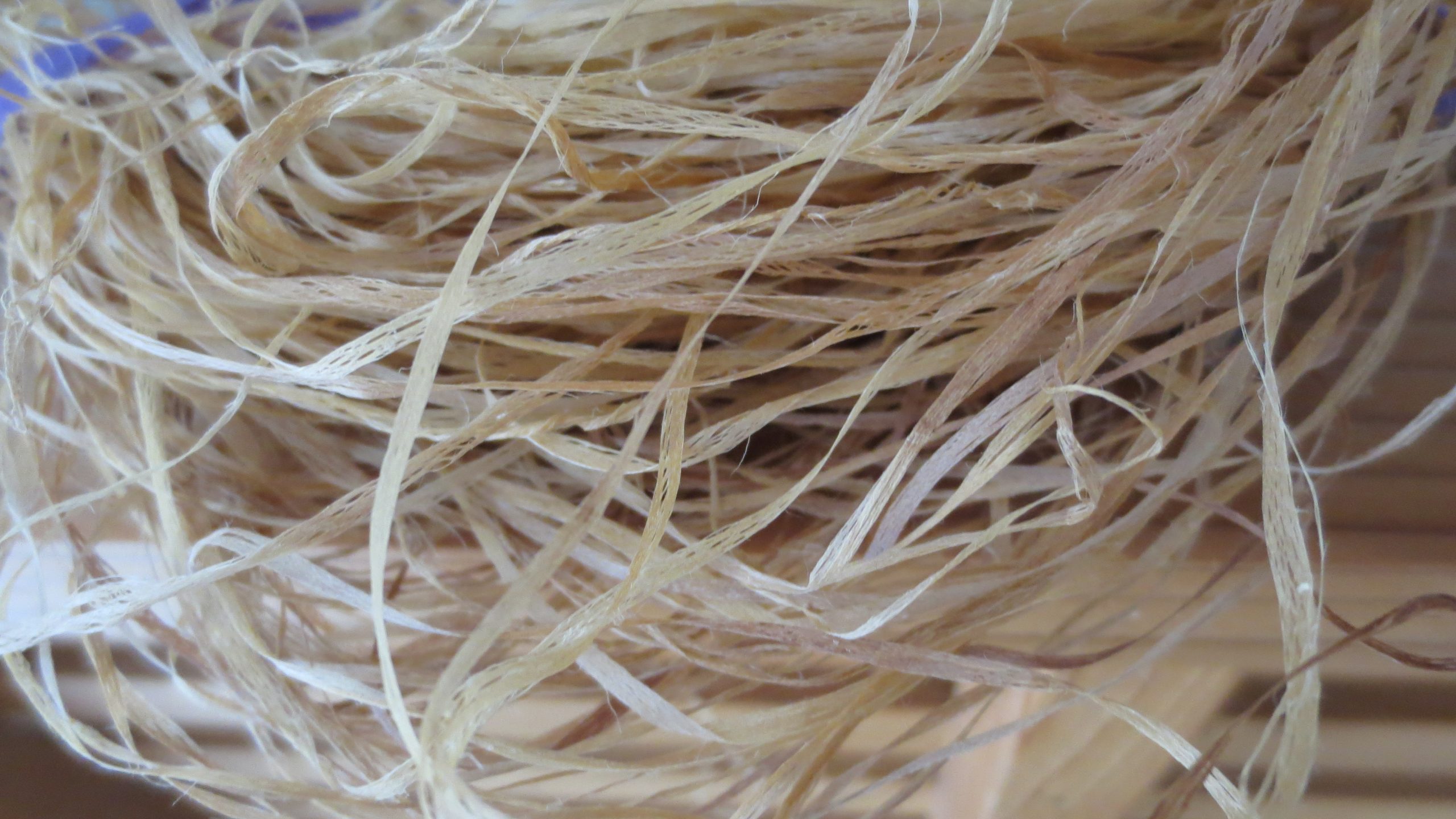
The split Shina linden fibers about 2m width
The split fibers are connected by twisting the ends together and spun into a yarn with additional twisting by a traditional twisting wheel. The twisting gives durability to the yarn. The warp and weft each have different twisting counts.
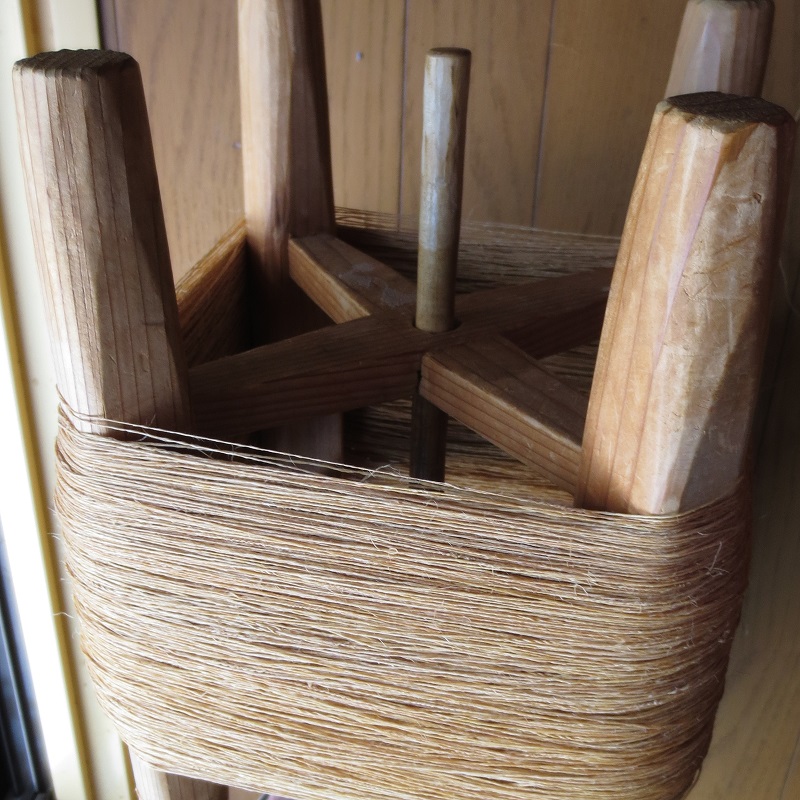
Shina-fu yarn wrapped up around a bobbin. Making it this far of spinning the yarn takes up almost all of the processes.
Finally, it is woven by a floor handloom. Shina-fu fibers need moisture for weaving it, so that weaving takes place during the heavy snow fall season of February and March.
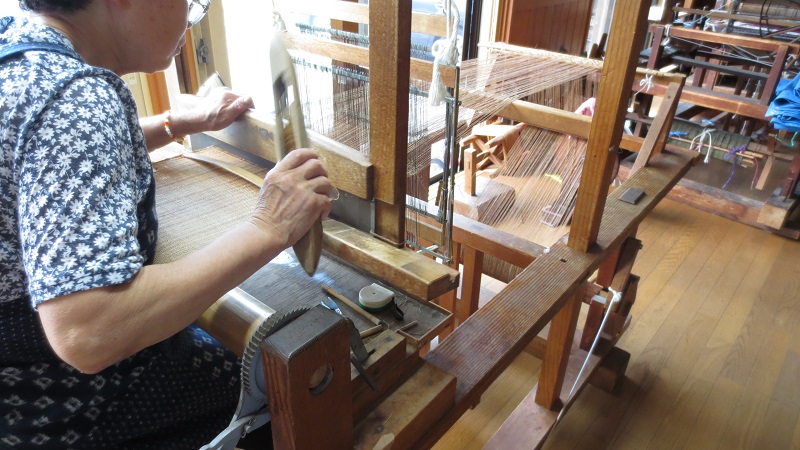
Shina-fu floor loom weaving. She is weaving Shina-fu more than 50 years.
As we have seen, it took almost a year to weave a bolt of Shina-fu linden fabric. All the processes are incorporated into their everyday living in the mountains.
In order to continue the tradition, not only keeping the technique of spinning and weaving, but also fostering natural good quality Linden trees is essential.
In the villages, the Shina-fu textile weaving tradition is a part of their lives, and respect their tradition by being remarkably faithful to the original techniques inherited from ancient time. It is almost a miracle that a prehistoric time’s folk life and textile tradition can be seen still today.

Shina-fu was used for a fishing net. The durability is extremely high.
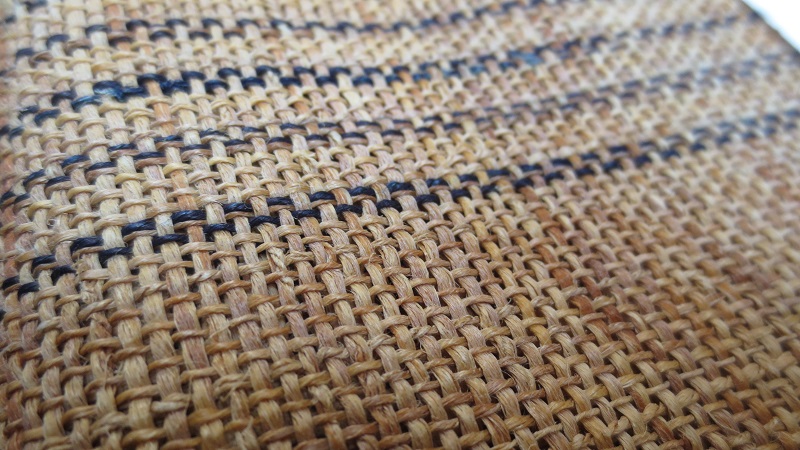
Shina-fu fabric woven for Obi (Kimono belt)